Cutting and joining
Cutting equipment
When textile material is transformed from its stock formStandard sizes for a material, component or product. (usually sheetA way to describe that a material is normally much thinner than it is long or wide. from a rollFlexible material wrapped around a tube or turned over and over on itself without folding.) into a product or garment, the term formingTaking fabric and using it to cut shapes that, once sewn, will become a 3D-formed garment. is used. These rolls of fabric come in standard widths of 90 cm, 115 cm, 150 cm, 200 cm or 240 cm.
Cutting this fabric must be accurate to ensure all patternShapes that, when cut from fabric and then sewn together, become a 3D textile product. pieces fit together on assembly, and the following equipment can be used to do this:
- fabric shears - sharp, have long blades and are designed to cut fabric easily and cleanly
- embroidery scissors - small, have a sharp pointed blade and are used for cutting intricate work
- pinking shears - prevent fraying, produce a zig-zag pattern along the edge of the fabric and are often used once a seam has been produced
In an industrial environment, fabric cutting equipment is far more robust because it has to deal with many plies of fabric:
- band knife or straight blade - a straight blade is used to cut through many plies of woven fabric
- round blade - a rotating cutter is used to cut through many plies of knitted fabric to prevent it from laddering
- die cutter - works like a pastry cutter stamping out shapes when pressure is applied and is used for simple shapes that don鈥檛 change as the dies are expensive to make, eg shoe insoles
- laser cutterA machine that uses a laser beam to vaporise material and cut out shapes very accurately. - an example of computer aided manufacture (CAM)The manufacture of a part or product from a computer aided design (CAD) using computer-controlled machinery, such as a 3D printer. and a quick method to cut out fabric pieces by directing a high-power laser beam, which then either melts or burns it, leaving a highly accurate cut edge or engraved patterns on the surface of the fabric
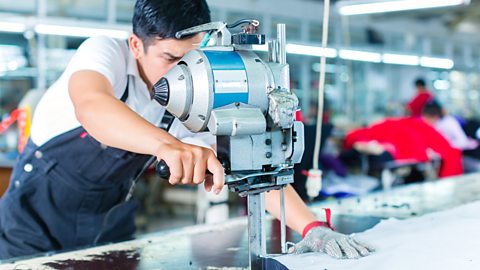
Joining fabrics
The most common method of joining fabric together is by sewing a seamA seam is usually 1.5 cm wide and is produced by sewing two pieces of fabric together. . There are three main types of seams used in the textile industry:
- plain seam - two pieces of fabric are joined together with a running stitch allowing for a seam allowance, which must be measured correctly to the desired width otherwise the garment being sewn will be the wrong size or shape, and needs neatening to prevent fraying (achieved by overlockingA stitch that sews over one or more pieces of fabric to prevent fabric fraying and is used to neaten seams once trimmed by an overlocking machine.)
- flat fell seam - very strong and required for textile products that are to be used, worn and/or washed a lot, seen on the right side of the fabric as two rows of stitching, eg on the inside leg seam of jeans
- French seam - sewn twice starting with the wrong sides of the fabric together, the first at a depth of 1.0 cm, trimmed and resewn at 0.5cm encasing the previous seam, self-neatening and used with fine fabrics to avoid becoming bulky
Image caption, Flat fell seam
Image caption, French seam
1 of 2
Fabrics can be shaped while being joined together:
- gathering - achieved by sewing two parallel lines of running stitch within the seam allowance to the top of a piece of fabric that can be pulled gently to ruffleA gathered piece of fabric. up the fabric and create fullness
- pleats - even folds of fabric are pressed and then sewn into place using a running stitch, often used to shape skirts
- darts - a triangle fold of fabric is stitched and used to shape a garment to fit the body snugly, found on the bust, waist or back of a top or dress, a dart is sewn on the wrongThe side of the fabric without the pattern that goes to the inside and is not seen. side of the fabric