Joining materials and components
Surface mounted technology (SMT)
surface mounted technology (SMT) Components that can be soldered directly to a board rather than having to be pushed through a hole. is used to place electrical components on top of circuit boards.
Advantages of SMT | Disadvantages of SMT |
Smaller components can be used | Not suitable for bigger electronic products |
Better performance | Connections can be damaged as constant heat is applied |
More reliable connections | |
More durable end result |
Advantages of SMT | Smaller components can be used |
---|---|
Disadvantages of SMT | Not suitable for bigger electronic products |
Advantages of SMT | Better performance |
---|---|
Disadvantages of SMT | Connections can be damaged as constant heat is applied |
Advantages of SMT | More reliable connections |
---|---|
Disadvantages of SMT |
Advantages of SMT | More durable end result |
---|---|
Disadvantages of SMT |
Soldering
soldering A method of joining, usually electrical components, by heating a filler metal called solder. When the solder cools, it fused the components together. can be done by hand or automated by machine. Solder is heated until liquid and then added to the components and printed circuit board (PCB) where it cools and sets, allowing electricity to flow from one point to another. Solder is an alloyAn alloy is a mixture of two or more elements, at least one of which is a metal. of lead and tin - it is a good conductor of electricity, does not rust and has a low melting point.
Image caption, Hand soldering
Image caption, Automated soldering
1 of 2
Pick and place assembly
pick and place assembly A robotic machine that is programmed to pick and place electrical components so they can be placed in the correct place on a circuit board. is when componentA part that when put together makes a product. are picked up and placed on a circuit board automatically by robots, with suction cups used to pick up and arrange components in the right place on the circuit board A copper sheet used to attach electrical components. . It is used in the production of printed circuit boards (PCBs) in electrical systems. Although buying the machines and programming them is expensive and time-consuming, their performance is quick and accurate, and it is also cost-effective when mass producing a circuit.
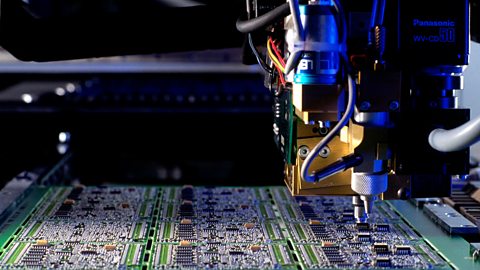
Manual assembly
Manual assembly of components can be fiddly and time-consuming, as components are small and take longer to fit into place when done by hand. This assembly method is used mainly for circuits made up of components that are fitted with pinThe pins on an integrated circuit appear in two rows and are manufactured as dual in line (DIL) packages. through a circuit board. This is a costly and slow method of production, more suitable for specialist production of small numbers of electronics such as for TVs, radios and alarms.
Flow soldering
flow soldering A solder paste is used to fix components in place until heated. The solder will only attach to an electrical pad because the rest of the board will be covered in lacquer. is a technique used to attach components to a circuit board. Components are placed on the PCB with pre-soldered pasted pads and are put into a precisely controlled oven where the solder melts into the correct position and an accurate connection is created.
- no need for human input
- accurate
- quick
- reduces the amount of solder used
Wave soldering
wave soldering A molten flow of solder is used to fix components in place. The solder will only attach to an electrical pad because the rest of the board will be covered in lacquer. is used in the mass production of PCBs as it is a fast, efficient and accurate way of soldering PCBs. Components are placed into a PCB by their pins through pre-drilled holes and put on a conveyor belt Used on a production line to move items along. - this takes the boards through a series of stages:
- flux Chemical used to improve the flow of solder. is added to the underside board to help the flow of solder
- it is then heated up and passed over a wave of solder
- the solder covers the pins under the PCB and creates a bond once cooled
Joining methods for materials
Joining methods are either temporary or permanent:
Temporary
- machine screw - a hexagon head with a threaded bar, used with a bolt to join wood, metals, plastics or a combination of materials together as a non-permanent join
- bolts - a hexagon shape, used to join materials
- wood screws - round headed, countersunk, Phillips or slotted and used to join metal and/or plastic to wood
Permanent
- pop rivets - used to join thin sheets of metal together
- welding - a strong join between two pieces of metal achieved by heating the pieces of metal and allowing them to fuse together as they cool
- brazing - a very strong join between two pieces of metal achieved by heating a filler, such as brass, between the materials